Welcome to Carbon Risk — helping investors navigate 'The Currency of Decarbonisation'! 🏭
If you haven’t already subscribed please click on the link below, or try a 7-day free trial giving you full access. By subscribing you’ll join more than 4,000 people who already read Carbon Risk. Check out what other subscribers are saying.
You can also follow my posts on LinkedIn. The Carbon Risk referral program means you get rewarded for sharing the articles. Once you’ve read this article be sure to check out the table of contents [Start here].
Thanks for reading Carbon Risk and sharing my work! 🔥
Estimated reading time ~ 10 mins
First published on E-FWD
Transformers are vital conduits to transport electricity from the point of generation to the point of consumption
The lead time for transformers has increased 10-fold since 2020, to around two years, while transformer prices have risen by almost 80%
Transformer supply is highly concentrated with little appetite among manufacturers to expand capacity
Around one-quarter of global renewable energy projects are thought to be at risk of delay due to the transformer shortage
The lifespan of transformer is 35-40 years, but many in use today are much older. Ageing transformers are highly inefficient, contributing to wasted energy
Transformers are the energy transition’s hidden supply chain challenge.
In contrast to the spinning blades of a wind farm, the army of electricity pylons stretching across the horizon and the vast array of solar panels seen on hillsides from afar, the humble transformer does not get the attention it deserves.
Boxed away in refrigerator-sized containers, the inner workings of the transformer are invisible. Yet without them, the energy transition is impossible.
Transformers are large pieces of electrical equipment built from a laminated steel core upon which are wound coils of copper wire. The main function of a transformer is to “step up” or “step down” the voltage of electricity using the principles of electromagnetism.
The voltage is increased to enable electricity to be transported long distances along transmission line with minimal losses. The voltage is reduced before the power is distributed to homes and businesses, ready to be used to power the appliances we need. Without the humble transformer, modern life would be impossible.
Surging demand hits fixed supply
Yet our dependency on the transformer is set to grow significantly over the next decade as two powerful trends – the energy transition and AI – look set to overwhelm supply.
Unbeknownst to many commentators who study these two emerging themes, the supply of transformers is already heavily constrained. The lead time to wait for delivery of a transformer has increased from 12-14 weeks pre-pandemic to 115-130 weeks in 2024.
The reason behind the surge?
The supply of transformers is fixed and highly price inelastic. Meanwhile, demand for transformers has surged. Utilities are rolling out renewable energy and technology companies are investing in vast data crunching capacity.
Meanwhile, transformer manufacturers have been hit by higher costs. For example, Grain Oriented Electrical Steel (GOES), used to produce the core of the transformer, has almost doubled in price since 2020. Meanwhile the cost of copper has increased by about two-thirds. Raw material costs account for around 45% of the total price of a transformer.
The upshot of the severe supply-demand imbalance and surging cost of raw materials is that the price of transformers has soared by 60-80% since the beginning of 2020.
Bullwhip effect
Another factor is the manufacturing base for transformers is highly concentrated.
Three large companies dominate the market: Germany’s Siemens Energy, US’ GE Vernova, and Japan’s Hitachi Energy. Once the electrical grid was largely built – roughly between the 1950s and 1970’s – the industry went into a period of consolidation.
Transformer manufacturers have been wary of over expanding their production capacity, for fear that demand might fall short of expectations.
Many firms were burnt by the housing crisis that followed the great financial crisis of 2008-09. Manufacturers that had expanded capacity anticipating house builds continuing – and hence increased demand for transformers – found themselves overextended when housing builds came to an abrupt halt.
Although transformer demand is dictated by similar technological dynamics, firms are also wary, given what has happened to the price of semi-conductors and PV cells during past periods of over-expansion. Manufacturers in these latter products have encountered volatile trading conditions, with periods of exuberance and despondency upsetting supply patterns.
Unlike semi-conductors and PV cells, transformers are bespoke pieces of kit. This means that it’s difficult to establish economies of scale in the same way that manufacturers of modular pieces of equipment enjoy. The bespoke nature also means that the availability of trained staff for both manufacturing and repair is limited.
Longer than expected
“There’s a real block on transformers,” Dorothy Thompson, former CEO of Drax and now board member at Eaton said earlier this year. “When I say block, we’re talking about lead times of 18 months to two years.”
Thompson noted a visit to an Eaton plant six years ago, “they were worried because they were making such low margins, [there was a question] of whether they should keep production going or should they rationalise? Fortunately they didn’t.”
Thompson, speaking at the Aurora Energy Forum, said people knew demand was coming for “grid reinforcement. But if you’re a manufacturer, you might know demand is there, but you have to be able to see it before you really invest. You’re not going to put scale investment in the supply chain until it really begins to materialise. Quite often in the energy transition, it’s taken longer to materialise than expected.”
Transformer delays slow the energy transition
Competition for turbine foundations, high-voltage cables and other components is likely to hamper the buildout of wind turbines, solar panels, and grid infrastructure across the UK, according to a recent report commissioned by the UK government.
The report, carried out by Baringa, also identified strong demand for transformers as a key supply chain constraint. This, it said, could have an impact on the development of the UK’s renewable energy capacity, as well as upgrading the power grid. “Transformer availability is a result of increasing demand from renewables projects, electricity networks, and industrial and commercial sectors,” it said.
Transformers are such an important piece of equipment that developers are reluctant to source equipment from suppliers they are not able to verify.
“There is also a reluctance to source transformers from non-European suppliers due to perceived reliability concerns. Transformers represent a single source of failure for wind farms, and a defective device can cause significant financial losses,” the report added.
The transformer market is heavily concentrated. But many of its vital components are even more heavily dependent on one or a small number of suppliers. For example, in Europe, the main suppliers of electrical steel are Germany, Sweden and Turkey.
However, competition from other energy transition demands coupled with geopolitical uncertainty has made the situation worse according to Baringa,
“There is also a shortage of electrical steel used for transformer cores due to competition from electric vehicle motors and the loss of Ukrainian and Russian manufacturing.”
It’s unclear to what extent UK renewable projects are directly affected by the high lead times involved in securing transformers. Wood Mackenzie has estimated that 25% of global renewable energy projects are at risk due to the shortage.
Transformers seeking efficiency
Stepping up and stepping down voltage contributes to transmission and distribution losses. The European Commission estimates that 2.9% of all energy generation wasted across the EU27+UK is a result of transformer losses. This is equivalent to 93 TWh.
Load losses are produced by the electrical current flowing through the copper coils and vary according to the load. No-load losses are caused by the magnetising current needed to energise the core. This second type of loss is constant irrespective of the load placed on the transformer.
Transformers are typically designed to last 35-40 years. More than 70% of transformers in the UK have been in operation for 25 years or more, according to Powerstar, a UK manufacturer of transformers. The firm believes that energy losses and the risk of an outage is significantly higher after just 20 years.
Increasing numbers of transformers are exceeding their design lifespan. Indeed, a freedom of information request submitted to the UK energy regulator Ofgem revealed the average age of a distribution transformer in the UK is 63 years old. Wilson Power Solutions, another UK manufacturer, submitted the request to Ofgem.
Technology shift
Old transformers increase the risk of down time, but they are also energy inefficient compared with newer versions. An ageing transformer is estimated to be around 85% efficient, although it may be even lower depending on its age and how it has been used.
In comparison, the energy efficiency of modern transformers can be as high as 99.75%.
Amorphous metal transformers (AMT), typically made up of Metglas, an alloy of iron with boron, silicon, and phosphorus, can eliminate up to 80% of the energy losses experienced by conventional transformers. AMTs require higher upfront costs compared with traditional steel core transformers. The operational energy savings offset this.
The move towards AMT has also been spurred by manufacturers concerned that they are overly dependent on GOES. Although amorphous cores utilise more readily available commodities such as silicon and iron, the global supply is also thought to be tight. Despite the benefits, manufacturers are wary of allocating the significant amounts of capital necessary to convert to AMT.
Regulation’s role
Eco-design regulations have also forced manufacturers to design new transformers with energy efficiency in mind.
EU regulations (EU No 548/20141 and Amendment (EU) 2019/17832) have introduced requirements for load and no-load losses for distribution and power transformers.
Tier 1 regulations came into effect in 2015, while Tier 2 followed in 2021 and incorporates stricter energy loss requirements. The UK also adopted Tier 2, despite Brexit.
The US is also tightening regulations. The Department of Energy (DoE) is currently consulting on measures to improve the energy efficiency of distribution transformers.
Despite the undoubted improvement in the energy efficiency of new transformers placed on the market, it will take decades to upgrade the hundreds of thousands of old, outdated, and inefficient transformers that are currently connected to the power grid.
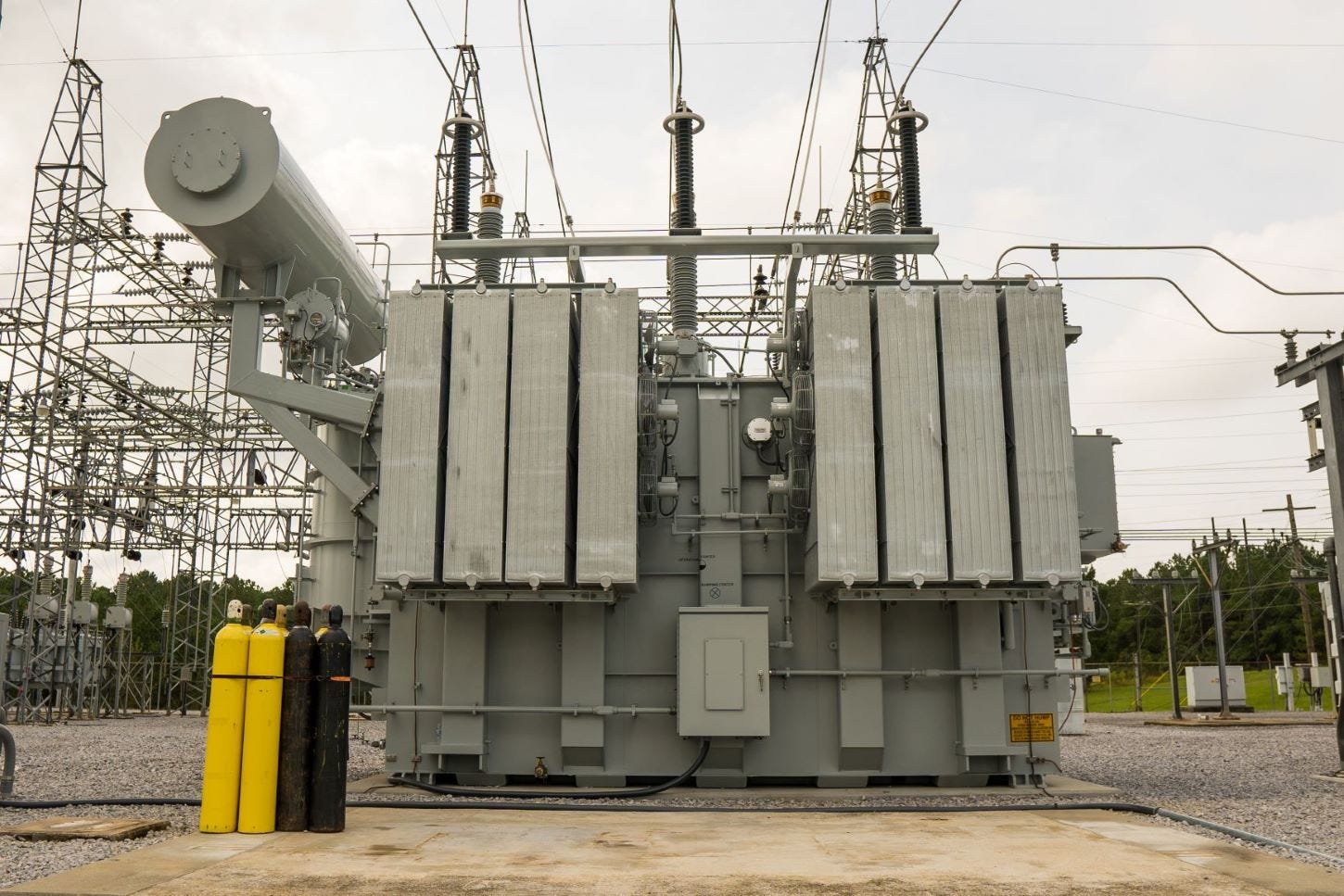
AI may eat transformers lunch
Demand is rising for electrification, feeding into demand for transformers. One of the drivers of new demand is data centres, springing up to feed AI.
Where there is a supply-demand imbalance, markets and technology inevitably find a way to resolve the bottleneck.
Indeed, AI may yet provide the answer to the transformer shortage. Indeed, one such solution is currently in development by a British tech start-up called IONATE. The firm has developed a smart grid solution. This aims to increase data visibility and real-time control of the flow of energy in electricity grids.
The company’s Hybrid Intelligent Transformer (HIT) replaces the passive transformer. Instead, in introduces a real-time control node, regulating voltage and reactive power with millisecond-level precision using magnetics.
In late 2023, Portuguese multi-national utility EDP announced a collaboration with IONATE. Under this agreement, the companies agreed to deploy in Portugal, Spain and Brazil, following a period of testing.
Announcing the collaboration, Luís Manuel, executive board member of EDP Innovation, commented on the potential to usurp conventional transformers. The HIT “has the potential to be a game-changer, replacing conventional passive transformers with state-of-the-art real-time control nodes”.
The mother of invention
It’s clear that transformers represent a major bottleneck to the energy transition. In contrast to specific shortages of equipment and materials that affect different parts of the energy transition in isolation, transformers affect everything.
The transformer industry is reluctant to invest for fear that the current demand surge is a one-off. However, on this occasion they may be misinterpreting the signals.
Government and corporate commitments to net zero suggests this is no ordinary boom.
There is new demand, for renewable energy and data centre connections. And this comes in addition to the backlog of inefficient transformers that must undergo repair and upgrading.
The extreme transformer supply-demand imbalance will be resolved somehow. Innovation will provide the answer and may even usurp the transformer industry as we know it. For the sake of the energy transition, it can’t come soon enough.
👋 If you have your own newsletter on Substack and enjoy my writing, please consider recommending Carbon Risk to help grow this amazing community of readers! Thank You!👍